Spraying foam insulation in cold weather presents unique challenges, but the right techniques and equipment can ensure success. Whether you’re working with open-cell spray foam or closed-cell spray foam, this guide provides actionable tips to overcome cold-weather hurdles and achieve proper foam adhesion.
Case Study: Open-Cell Spray Foam in Cold Conditions
An applicator encountered issues while spraying open-cell spray foam on a wood construction project with outside temperatures of 30°F. A kerosene heater raised the ambient temperature to 42.4°F, and the contractor believed they had surpassed the necessary 5°F difference between the dew point and substrate temperature. Yet, the foam was pulling off the walls.
What went wrong?
Using a thermal gun, they found the substrate temperature was only 29.2°F, creating just a 2°F difference from the 27°F dew point. This small temperature gap caused foam adhesion issues, leading to spider webbing in the insulation.
Solution:
• Use infrared heaters to warm the substrate without introducing excess moisture.
• Start spraying at the highest point in the building, working downward to avoid areas where evaporation gathers.
• Apply ½”-1” flash passes to promote adhesion on cold substrates (though this may reduce yield).
Best Practices for Spraying Foam Insulation in Cold Weather
1. Precondition Materials
• Store materials in a controlled environment at 70-80°F for several days before application.
• Maintain drum temperatures in the same range using band heaters, blankets, or infrared heaters. Avoid direct heat over 80°F to prevent boiling off the blowing agent.
2. Balance Processing Temperatures
• Run resin preheat temperatures 2-3°F higher than the A-side and hose temperatures.
• Verify that foam is processed in a 1:1 ratio by checking pressure gauges and product density.
• Spray continuously for 10 minutes after adjusting temperatures to stabilize conditions.
3. Address Substrate and Environmental Factors
• Use infrared heaters in metal buildings to prevent condensation caused by kerosene or diesel heaters.
• In wood buildings, limit the amount of heat and moisture added when using fuel-burning heaters.
• Start spraying on the sunny side of the building to work on the warmest areas first.
• Use a smaller mixing chamber to concentrate heat and maximize foam expansion.
Key Equipment for Cold Weather Spray Foam Success
Investing in reliable equipment ensures optimal performance in challenging conditions. Every contractor should have:
• Thermal Gun: Measure substrate and material temperatures accurately.
• Temperature & Humidity Meter: Monitor ambient conditions to confirm suitability for foam application.
• Moisture Meter: Check substrate moisture levels to prevent adhesion issues.

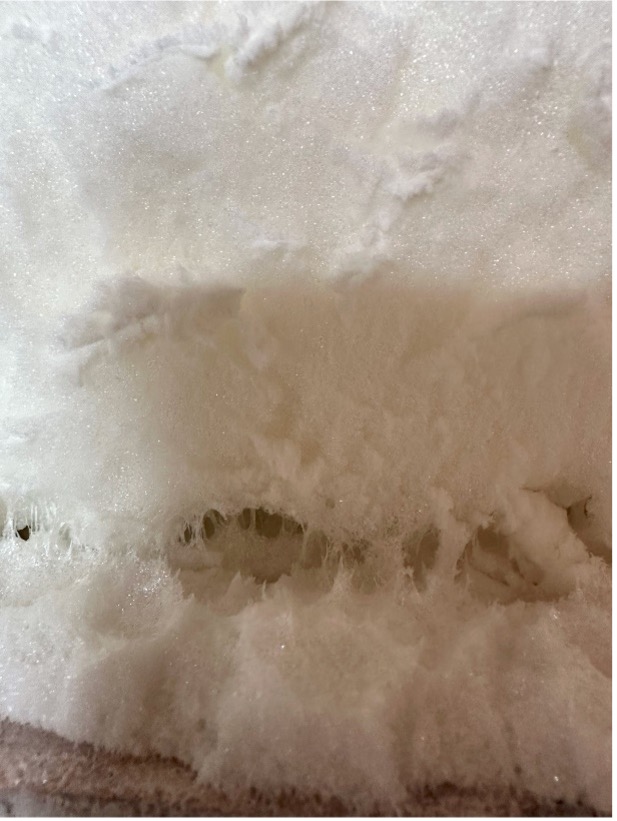
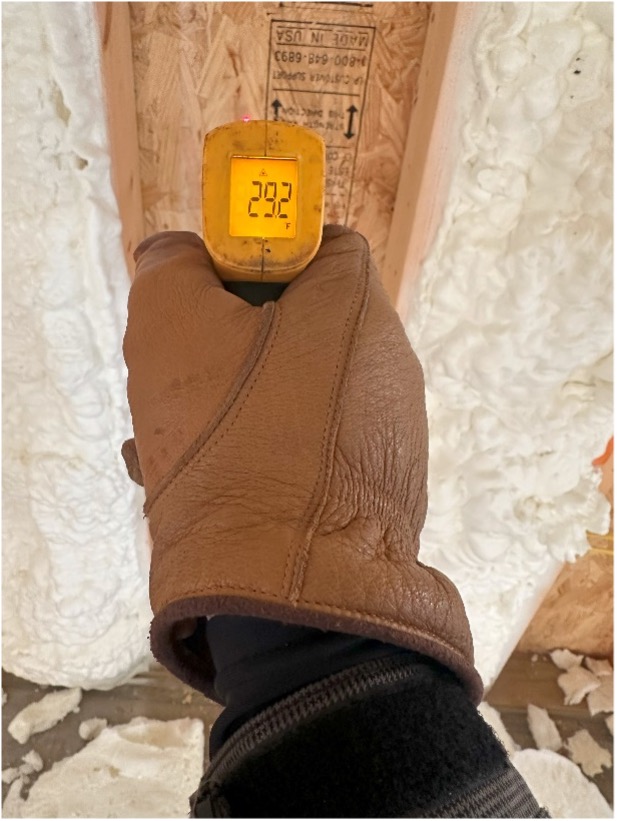
Case Study: Closed-Cell Spray Foam in Cold Weather
On a closed-cell spray foam project, a contractor faced pressure imbalances and sluggish foam performance. While the drum’s exterior temperature was 82°F, a thermal gun revealed the material at the drum’s center was only 50°F. This discrepancy affected the foam’s performance.
Lesson Learned:
Exterior drum temperatures may not reflect internal material temperatures.
Solution:
Precondition material in a controlled environment to ensure consistent temperatures throughout the drum.
Final Tips for Spray Foam Insulation in Cold Weather
1. Apply Thin Layers: Use flash passes of ½”-1” for better adhesion to cold substrates.
2. Minimize Stopping: Spray continuously for at least 10 minutes to maintain consistent product temperatures.
3. Choose the Right Heater: For metal buildings, prioritize infrared heaters over kerosene or diesel to avoid condensation.
4. Optimize Your Workflow: Start with warmer substrates, such as the sunny side of the building.
By applying these tips, you can achieve high-quality results even in extreme cold. Whether you’re spraying open-cell or closed-cell spray foam insulation, preparation and proper equipment are key to success.
For expert advice, premium materials, and unmatched technical support, partner with IPS. We help contractors and applicators spray with confidence, no matter the season.
FAQs
Q: What is the minimum temperature for spraying foam insulation?
A: While specific temperature thresholds vary by product, it’s essential to maintain a minimum 5°F difference between the substrate temperature and the dew point. Always check the manufacturer’s processing parameters for the recommended ambient and substrate temperature ranges.
Q: What happens if the substrate is too cold?
A: Cold substrates can cause poor adhesion, shrinking, or “spider webbing” in the foam. Using infrared heaters to warm the substrate and applying thin flash passes (½”-1”) can help improve adhesion in these conditions.
Q: Why is a thermal gun necessary for cold-weather applications?
A: A thermal gun accurately measures substrate and material temperatures, helping you ensure the environment is suitable for foam application. Relying on ambient temperature alone can lead to errors, as substrate and material temperatures may differ significantly.
Q: How can I prevent condensation on metal buildings during foam application?
A: Use infrared heaters to warm metal substrates without adding moisture. Avoid kerosene or diesel heaters in metal buildings, as they can cause condensation and affect foam adhesion.